From Prototype to Mass Production: Scaling Your Hardware Product
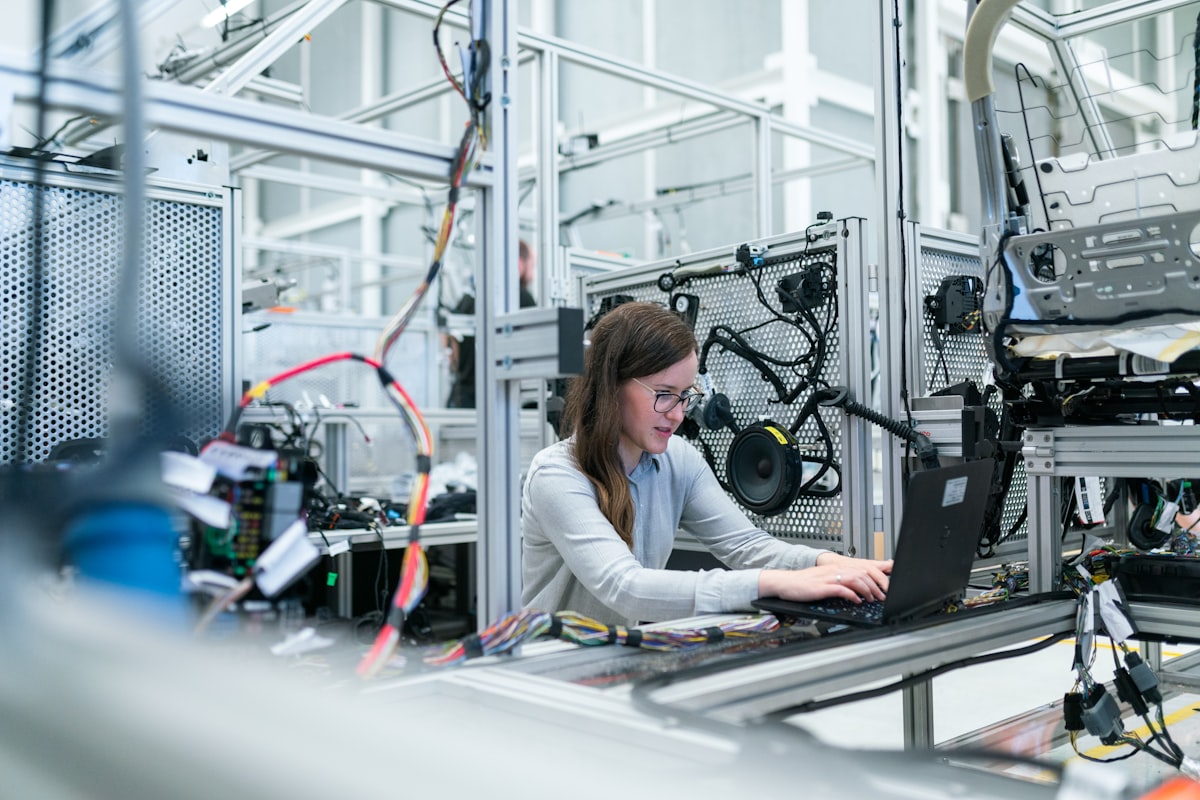
Taking a hardware product from a working prototype to mass production is one of the most challenging transitions in product development. Having guided hundreds of products through this journey across our facilities in Shenzhen, Amsterdam, and New York, we've developed a systematic approach that minimizes risk and accelerates time-to-market.
The Five Stages of Hardware Scaling
Understanding these distinct phases helps you plan resources, timeline, and budget effectively:
1. Proof of Concept (POC)
Your breadboard or development kit prototype proves the concept works. Key goals:
- Validate core functionality and user experience
- Identify technical risks and unknowns
- Gather initial user feedback
- Define key specifications and requirements
2. Engineering Validation Test (EVT)
First custom PCB, typically 5-10 units. Focus areas:
- Schematic verification and circuit optimization
- Component selection for performance and cost
- Initial thermal and power consumption testing
- Firmware development and debugging
3. Design Validation Test (DVT)
Refined design, 50-100 units. Critical validations:
- Mechanical integration and enclosure fit
- Environmental testing (temperature, humidity, vibration)
- EMC pre-compliance testing
- Battery life and power optimization
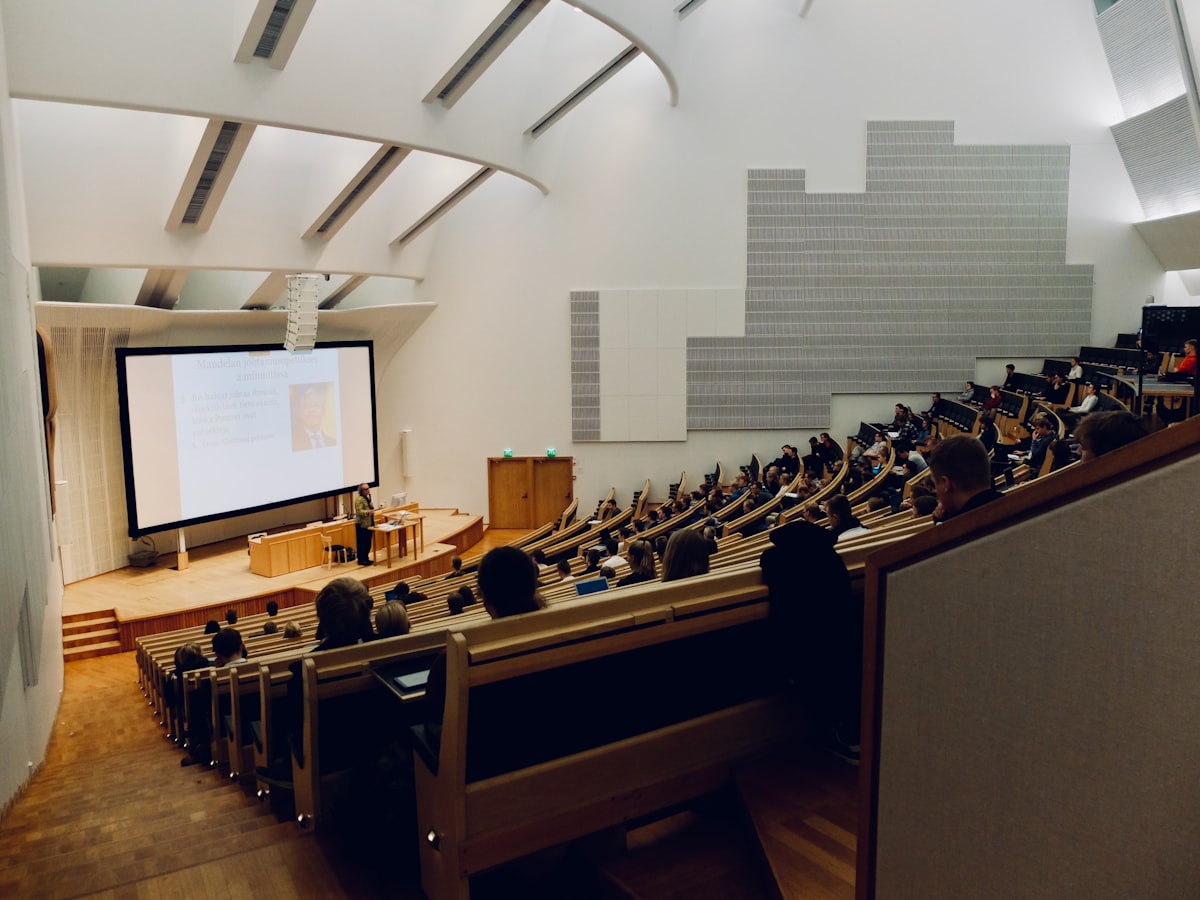
4. Production Validation Test (PVT)
Production-ready design, 500-1000 units. Final checks:
- Manufacturing process validation
- Assembly time and yield optimization
- Quality control procedures
- Certification testing (FCC, CE, UL)
5. Mass Production (MP)
Full-scale manufacturing. Ongoing activities:
- Supply chain management
- Quality assurance and yield monitoring
- Cost optimization
- Continuous improvement
Design for Manufacturing (DFM) Principles
Every decision during development impacts manufacturing efficiency. Here's what our production engineers prioritize:
Component Standardization
- Common values: Use E12/E24 series for resistors and capacitors
- Package consistency: Standardize on 0603 or 0402 throughout design
- Supplier diversity: Specify components with 3+ qualified suppliers
- EOL awareness: Check component lifecycle status early
Assembly Optimization
Reduce assembly time and improve yield:
- Place all SMT components on one side when possible
- Group components by type and value for efficient pick-and-place
- Use pin-in-paste for through-hole components to eliminate wave soldering
- Design in panel arrays with appropriate break-away tabs
Test Strategy
Build testability into your design:
- Bed-of-nails: Add test points on all critical nets
- Boundary scan: Use JTAG for complex digital designs
- Built-in self-test: Implement firmware test modes
- Functional test: Design fixtures for end-to-end validation
Supply Chain Excellence
A robust supply chain is the backbone of successful scaling. Our global presence provides unique advantages:
Strategic Sourcing
- Direct relationships: Work with component manufacturers, not just distributors
- Buffer stock: Maintain 3-6 months of critical components
- Alternative sources: Qualify second sources for all critical parts
- Price stability: Lock in pricing with quarterly forecasts
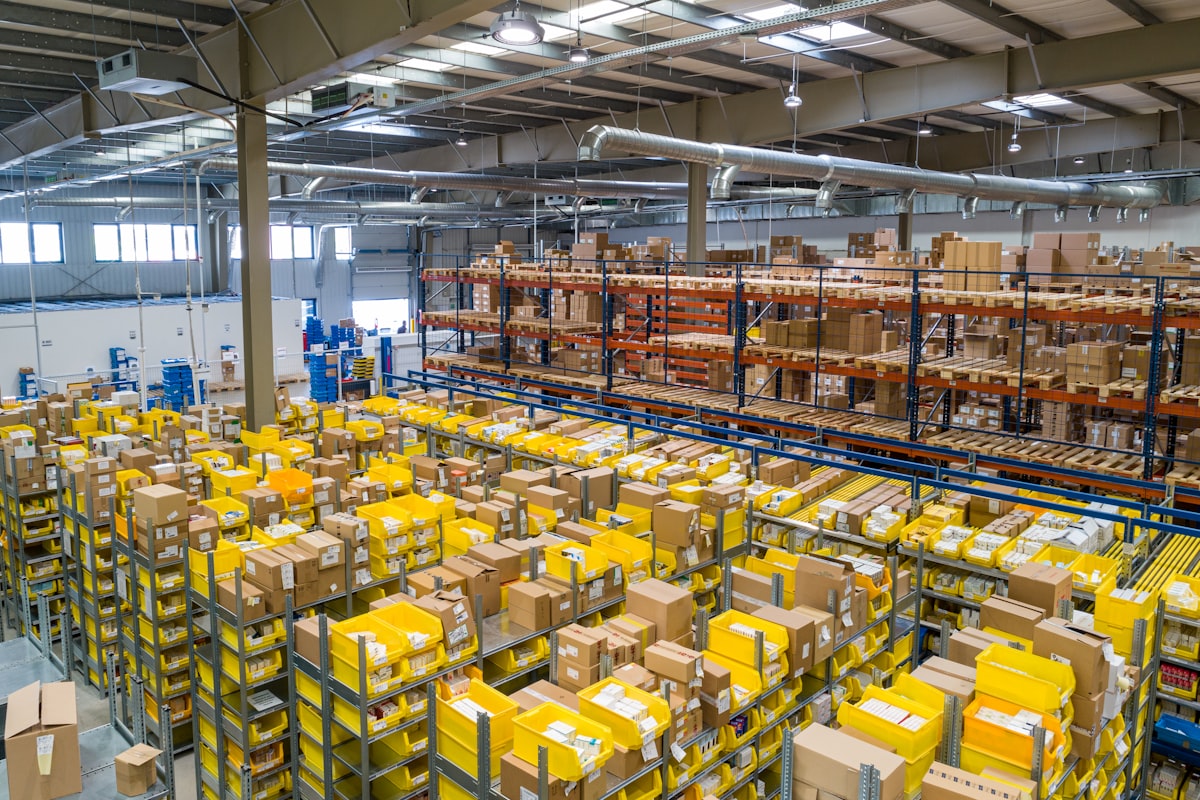
Risk Mitigation
Protect against supply chain disruptions:
- Monitor component availability trends and EOL notices
- Maintain approved vendor lists (AVL) with alternatives
- Use generic components where possible (resistors, capacitors)
- Consider geographic diversity in component sourcing
Quality Control Systems
Quality isn't just testing - it's a comprehensive system:
Incoming Quality Control (IQC)
- Sample inspection based on AQL standards
- Component authenticity verification
- Moisture sensitivity level (MSL) management
- First article inspection for new components
In-Process Quality Control (IPQC)
- SMT placement accuracy checks
- Reflow profile monitoring
- AOI (Automated Optical Inspection) after SMT
- X-ray inspection for BGA/QFN packages
Outgoing Quality Control (OQC)
- 100% functional testing
- Sampling for environmental stress testing
- Cosmetic inspection and packaging verification
- Traceability documentation
Cost Optimization at Scale
Moving to mass production opens opportunities for significant cost reduction:
Volume Pricing Benefits
- Components: 30-50% reduction at 10K+ quantities
- PCB fabrication: 40-60% reduction with panelization
- Assembly: 20-30% reduction through automation
- Testing: 50% reduction with optimized fixtures
Design Optimizations
- Reduce layer count through careful routing
- Minimize unique component count
- Use standard PCB sizes and thicknesses
- Design for automated assembly and testing
Common Scaling Challenges
Learn from these frequent issues we help clients navigate:
- Underestimating lead times: Plan 16-20 weeks for first production run
- Component obsolescence: Always have second sources identified
- Certification delays: Start compliance testing during DVT phase
- Yield issues: Design margin into your specifications
- Cash flow: Production requires significant upfront investment
Your Path to Mass Production
Success in hardware scaling requires expertise, relationships, and infrastructure. Our integrated approach combines:
- Engineering support in New York for design optimization
- Project management in Amsterdam for coordination
- Manufacturing excellence in Shenzhen for production
Whether you're planning your first 1,000 units or scaling to millions, we provide the expertise and infrastructure to make your hardware vision a reality.
Ready to scale? Contact us at rfq@source.parts for a manufacturing readiness assessment and production quote.